Process parameter optimization by Fraunhofer IAPT
Fraunhofer IAPT scales high-productivity L-PBF process for complex automotive component
In a joint research project with Constellium, Fraunhofer IAPT has successfully demonstrated the feasibility of high productivity L-PBF processing of the aluminum alloy AHEADD® CP1. Fraunhofer IAPT built an automotive door hinge demonstrator at 145 cm³ / h, using an industrial single-laser L-PBF system.
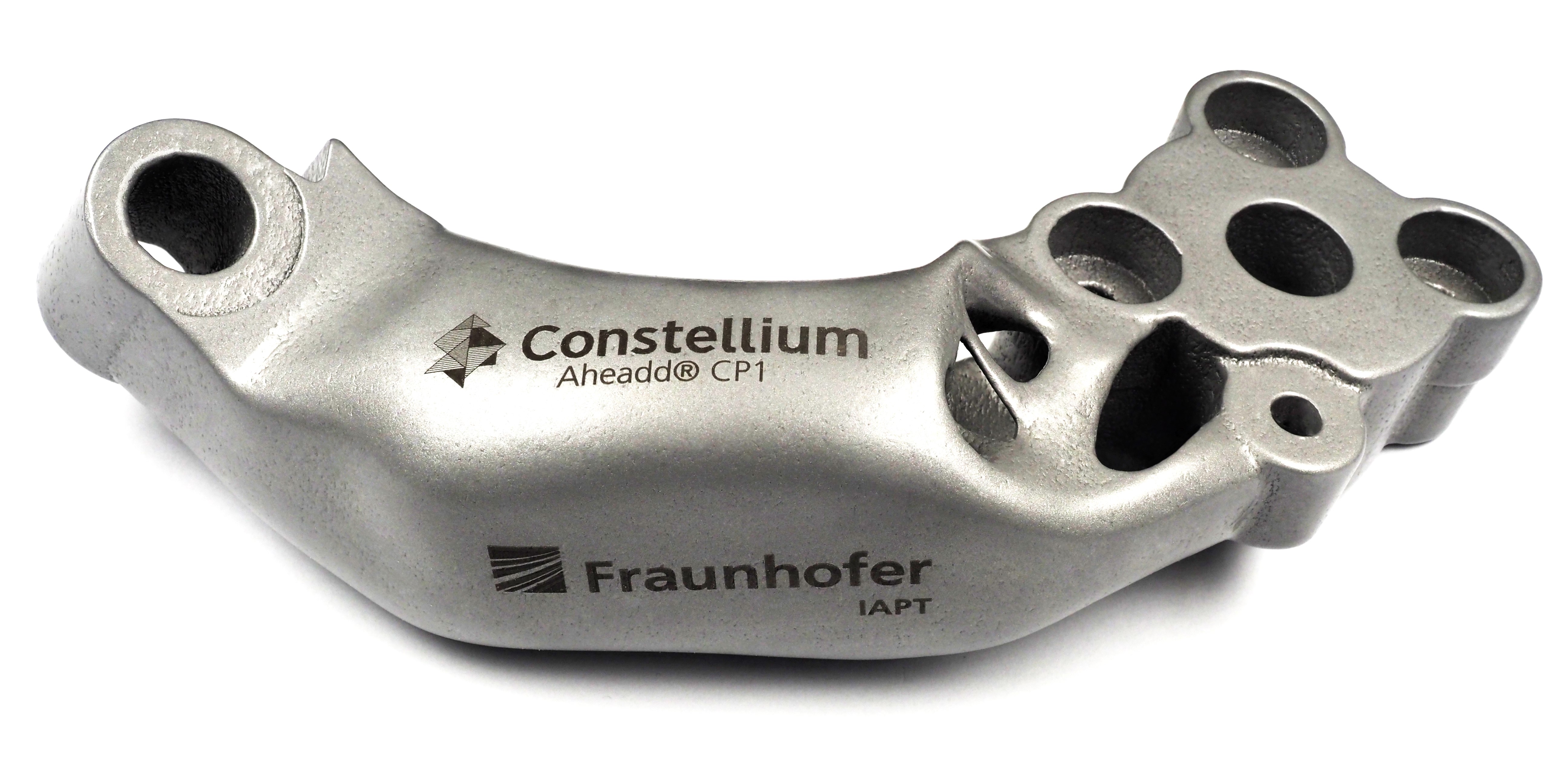
In the initial project phase Fraunhofer IAPT developed a process to obtain highly dense material samples using an industrial L-PBF setup with a 1kW laser system. It was found that build-up rates up to 164 cm³ / h could be achieved using suitable combinations of high layer thickness, laser power, scan speeds and hatch distances. Density in all specimens remained constantly higher than 99.7 %. Tensile tests showed ultimate tensile strength values > 300 MPa and yield strength > 270 MPa.
In addition to the initial study, the Fraunhofer IAPT team developed the initial set of surface parameters to assess the surface roughness properties of the alloy. Contrary to the standard L-PBF aluminum alloy behavior, the roughness did not vary drastically between vertical and horizontal surfaces. 120µm layer thickness builds gave Ra values in the range of 22 µm to 32 µm. Such a minor difference in Ra value variation is expected to provide a considerable advantage to design high-performance components with good fatigue properties.
While tripling the process speed compared to the standard processes, alloy density and sample properties remained well within the expected range. Therefore the Fraunhofer IAPT engineers transferred the results to a topology optimized automotive hinge designed for L-PBF. This component had been manufactured previously in a standard AlSi10Mg alloy using conventional process parameters with a layer thickness of 60 µm and build-up rate of 40 cm³ / h.
For the benchmark build job, a build-up rate of 145 cm³ / h was chosen. The part was built on an industrial 1kW laser system. Accompanying tests showed that a density of 99.8 % was achieved. Following the build job, the part was post-processed in a combination of vibratory finishing and blasting. The finished component is shown in Fig.1. Fraunhofer IAPT’s team successfully demonstrated the potential to transfer high-speed process parameters to a real use case in an industrial setting. In the next steps, dynamic loading behavior of the material will be validated to confirm suitability of the process for structural applications.
Considering that the present development was conducted on a single laser system, a potential transfer of the parameters to multi-laser systems will further increase productivity and help decrease part costs. As a result, additive manufacturing will continue to become more attractive for economic and sustainable production of complex lightweight and functional automotive components.